We entered our product in a thin film damage competition held by the prestigious Lawrence Livermore National Laboratory in California, the Thin Film Laser Damage Competition and won multiple times in a row. The event is held every year as part of SPIE Laser Damage, which is the annual meeting for laser damage materials and thin films used with high energy and high power lasers.
Laser damage is defined as any permanent change in the coating after exposures to lasers. The damage must be detected by scattered light offline or by offline microscopy.
The competition was anonymized. Testing was performed by LIDARIS, which provides world-class optics testing services. SPIE Laser Damage 2021 was an online event under the circumstances, and we sent in our samples to be tested.
This competition was a follow-up to the 532 nm nanosecond laser mirror thin film damage competition held in 2020. It was held to test available high reflector coatings with laser delivered in the visible light spectrum.
Requirements of the competition
The competition involved a double blind laser damage test to find out the laser damage resistance of 515 nm mirror thin film. The laser used was in the femtosecond pulse region. All mirrors entered were normal incidence multilayer mirrors.
There were certain other specifications that competitors were required to follow, such as:
- Reflectance of greater than 99.5%, which is the standard for normal incidence mirrors.
- An incidence angle of zero degrees.
- A wavelength of 515 nm.
- Pulse length of 200 femtoseconds
- Repetition rate of 5 kHz
- An environment of ambient air
There were no group delay dispersion (GDD) specifications, no stress or wave-front requirements, and no surface quality requirements. It was up to us contestants to choose the design, deposition method and materials for the contest.
The fs-laser source available for testing delivered pulses at 515 nm.
The double blind test made sure all contestants and samples were anonymous.
The testers used two damage criteria for laser induced damage: catastrophic damage and color change. Catastrophic damage refers to degradation of the laser. During the test, a single site was exposed to a number of pulses (either 1 or 1000). Color change usually refers to a subtle change in the appearance of the coating, that can be observed using microscopic enhanced-contrast images.
Our Submission
Along with our submission, which was codenamed Indigo for the double-blind test, we were required to submit details on the number of layers and coating materials on our thin film mirrors. We were also required to submit reflectance or transmission spectral scans in the 400 to 600 nm range. We also included a brief description of the deposition method we had used, along with the substrate material and the cleaning method.
The Results
As you can see in the chart below, our product ‘Indigo’ left the competition far behind with its performance on the LIDT test. Our thin films were able to withstand laser fluence of 130 J/cm2 before starting to degrade. The test results proved that our coatings are able to withstand high laser energy and prove that we put our money where our mouth is. Our thin film optics and coatings have been developed to be state-of-the-art and to withstand the high power high energy applications that are gaining ground in medicine and other fields today.
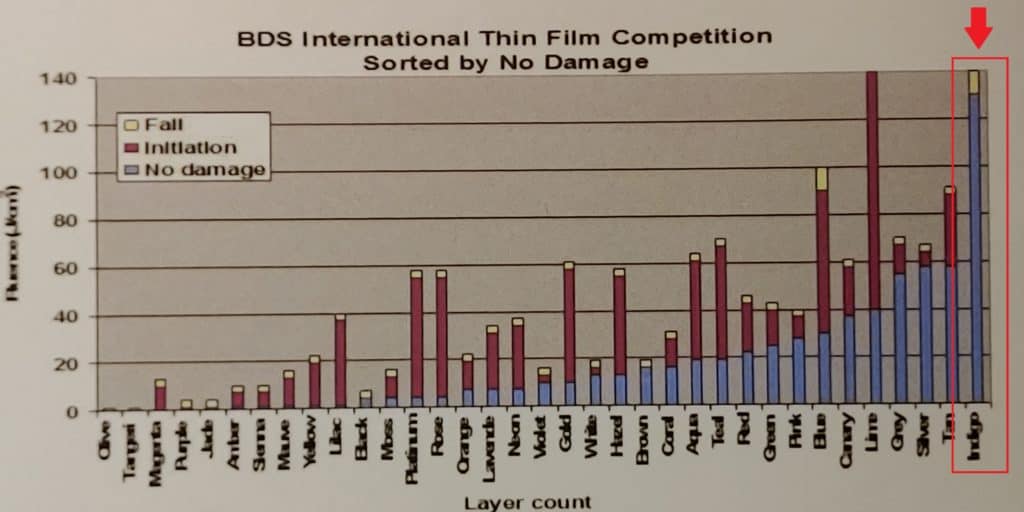
We are proud of our track record
In light of this win, we are proud to share our achievements with readers, customers and suppliers, without whom our business success wouldn’t have been possible.
Preferred Supplier Awards, Quality and Delivery
We have been recipients of the Preferred Supplier Awards, for Quality and Delivery. These awards recognize the outstanding value, service, strategic value-addition, innovation and collaboration that we’re capable of and extend to our customers and business partners.
Super Polished Laser Crystals and Optics
We are providers of super polished optics and laser crystals with ultra-low surface roughness. Super polished optics help to keep surface scatter to a minimum. This is valuable in lowering laser damage and increasing laser efficiency in applications. We are fully equipped to meet the emerging demands of ultraprecision optics and laser crystals, driven by laser fusion, space optics and semiconductor industries looking for high precision form accuracy and super smooth surfaces. Our technology enables us to bring roughness down to negligible amounts.
90 Day Salt Fog Test
Our products have withstood the 90-day salt fog testing time and again, proving that they can be used in the harshest of environments. The salt fog test or salt spray test is the standardized method for the durability of protective coatings. The sample is placed in a closed chamber and exposed to a dense metal fog similar to harsh, corrosive environments.
The natural corrosion process is more complex than any experimental setting, but the results give us a ballpark estimate of a sample’s corrosion-resistance. The test value helps us to compare corrosion resistances of various coatings.
With our specialized coating technology, we can overcome the longstanding issues of durability and loss of transmission especially in the harsh environments of military operations. Our optics have the ability to operate dependably over a long period of time.
2008 Laser Damage Symposium in Boulder 130J/cm2
We have been participating at the SPIE symposia for some time now. At the 2008 Laser Damage Symposium at Boulder, we were able to showcase high laser damage thresholds of 130J/cm2 for our optical products.
Final thoughts
The field of semiconductors and high power lasers is gaining ground as applications are broadening across various industries. Our laser crystals and optics are widely used in eye surgery and stone removal, metal processing, environmental instrumentation measurements, optical transmission systems, and more. Our products are used in HoLEP equipment, range finding equipment, material processing and more.
Our endeavor is to always meet and exceed the expectations of our customers as we strive to continually improve our products. Our achievements in offering state-of-the-art laser crystals and optics would not have been possible without the support of our customers and business partners.